Gear Pumps
Because one size does not fit all
What is a Gear Pump?
A Gear Pump, also called a positive displacement pump, or a spin pump, consists of two inter-meshing gears within a metal housing. These gears rotate within the spin pump housing creating pressure that pushes the fluid through the pump, a process commonly referred to as positive displacement. The pumped product fills the space between the gear teeth and the spin pump housing and moves around the gear, much like a waterwheel. The size of the gear teeth and the speed at which they rotate determines the quantity of product metered and pumped. This process allows for highly accurate and measured amounts of fluid to be metered and transferred, commonly known as “positive displacement metering”. Mahr Precision Gear Pumps maintain their high wear resistance and absolute dimensional stability, even under extremes of temperatures, pressures and viscosities.
What is a Positive Displacement Pump?
A positive displacement pump is a type of pump that transfers liquid through the action of gears, screws, vanes, plunger, piston, or diaphragm. There are two main types of positive displacement pumps; Rotary and Reciprocating.
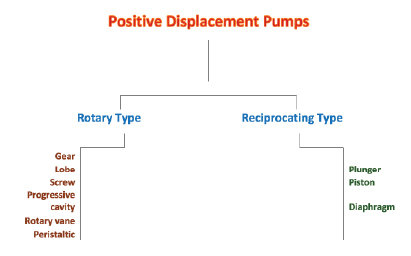
Rotary Pumps
The rotary pump category includes the most famous types of positive displacement pumps. These pump types use a rotating component to move the liquid. This rotary movement transfers the liquid from the storage tank to the delivery pipe. The most popular types of rotary positive displacement pumps are Gear, Lobe, Screw, Progressive Cavity and Rotary Vane.
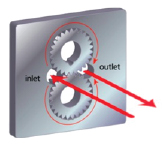

Reciprocating Pumps
A reciprocating pump works by the repeated back & forth movement of either a plunger, piston or diaphragm. These “strokes” or cycles are commonly referred to as reciprocation.
4 MAIN REASONS FOR USING A POSITIVE DISPLACEMENT PUMP:
WHY POSITIVE DISPLACEMENT PUMPS OVER OTHER TYPES OF PUMPS?
There are several advantages of positive displacement pumps over other types of pumps such as piston pumps, progressive cavity (screw pumps), or peristaltic pumps:
ADVANTAGES & DISADVANTAGES OF A POSITIVE DISPLACEMENT GEAR PUMP
Advantages
Disadvantages
PUMP TYPE & RATING FOR VARIOUS FLUID CHARACTERISTICS
Gear | Lobe | Screw | Progressive Cavity | Rotary Vane | Peristaltic | |
---|---|---|---|---|---|---|
>100C | 5 | 5 | 5 | 2 | 4 | 2 |
Abrasives | 2 | 3 | 3 | 5 | 2 | 5 |
Pressure | 5 | 4 | 4 | 2 | 3 | 2 |
Chemical | 5 | 5 | 5 | 2 | 3 | 2 |
Shear | 2 | 4 | 2 | 5 | 2 | 5 |
Particulates | 1 | 3 | 2 | 4 | 2 | 5 |
CIP | 1 | 5 | 2 | 5 | 2 | 5 |
Sanitary | 1 | 5 | 1 | 5 | 1 | 5 |
Accuracy | 5 | 4 | 4 | 4 | 2 | 4 |